When making electrical connections, one of the most critical aspects is soldering. Also, the soldering process is inevitable in joining almost all electronic components. But what exactly does this process entail? What are some of the key considerations during soldering? What are the different types of Solder?
Types of Solder by Composition
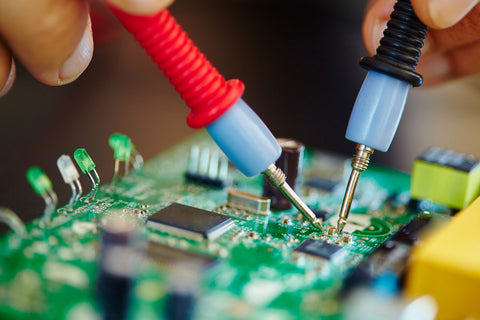
Figure 1: Man working in an electronic laboratory
Lead-Based Solder
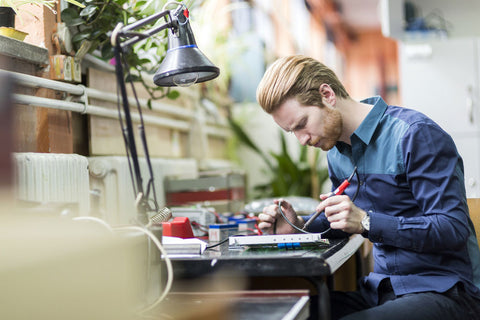
Figure 2: A Young Man Soldering a Circuit Board
It is the most common type of solder. As the name suggests, its primary metal is Lead. Also, it’s the best type of SSolder due to its impressive wetting and mechanical features. The table below gives the various types of Lead alloy solders.
Lead-free Solder
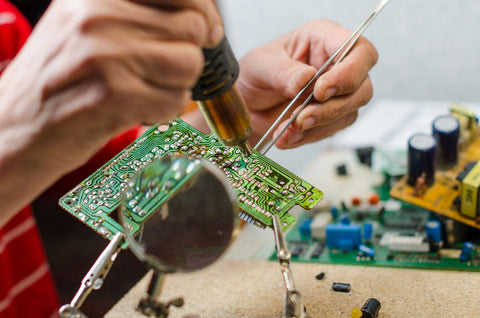
Figure 3: Engineer soldering a microcircuit
Note, Tin here is the primary metal. Others such as copper and silver are available in trace amounts.
Essentially, such SSolder complies with RoHS (Restriction of Hazardous Substances) regulations.
The common types of this fusible alloy include the following:
Additionally, you can consider SAC387 and SAC405 as eutectic. Materials with such characteristics share a melting temperature. In the case of these solders, they have a melting temperature of approximately 217°C.
Flux-Core Solders
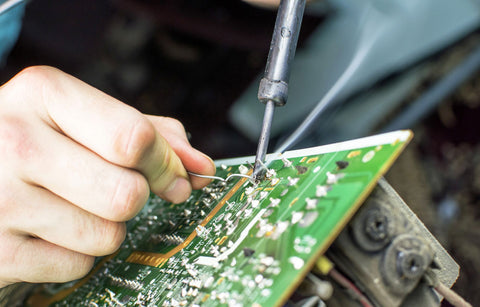
Figure 4: The process of soldering microcircuit TV using a soldering iron
A flux core solder is similar to leaded solders’ appearance as both are cylindrical. Also, you’ll find a reducing agent at the solder core. When soldering using these forms of SSolder, you activate the release of the flux.
Note that the commonly used material is rosin flux during electronic components soldering. Alternatively, acid cores are the primary flux for plumbing and metal enjoining applications.
Silver Alloy Solders
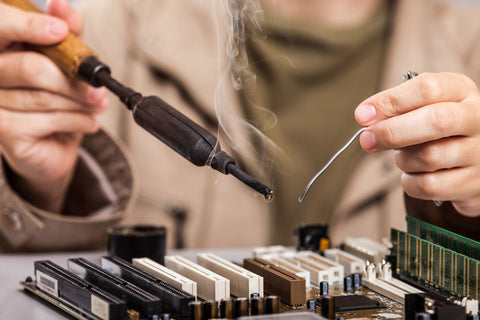
Figure 5: Soldering Process
Silver solders can be lead-based or lead-free. The aim was to prevent the silver migration effect that renders the joints brittle.
Note, the proportions of the silver and other alloys are varied. Thus, the price and mechanical strength of the alloys rely on the ratios of the metals.
Types of Solder by Core Style
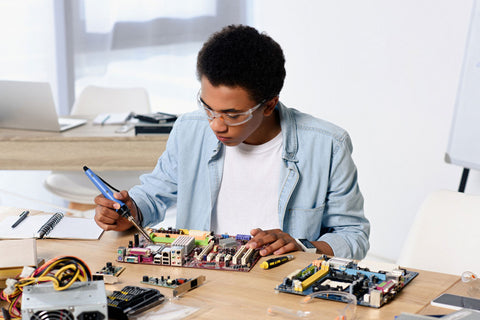
Figure 6: A Student Soldering
In this mode of classification, there are three major types of soldiers. They include the following:
Acid Core Solder
It consists of a wire wound on a hollow core with an acid-based flux. Since it is acidic, the change can cause aggressive activity on the target metal’s oxide layer.
Joints with high tensile strength characterize the flux. In addition, Solder is joint in joining metals and steel because of its corrosion resistance. You’ll also find these solders on copper pipes, and other standard plumbing uses.
Rosin Core Solder
It is similar in structure to the Soldier above in that both have a hollow core. Nonetheless, a resin flux is milder than the acid core for this Solder. The Solder is also corrosion-resistant. Additionally, it will form a permanent bond in electrical connections. Thus, it is shared as an electrical solder.
Solid Core Solder
Unlike the two soldiers we’ve discussed, It is a solid material of an alloy without a flux. Therefore, to create solder connections, you’ll have to introduce change.
Types of Solder by Form Factor
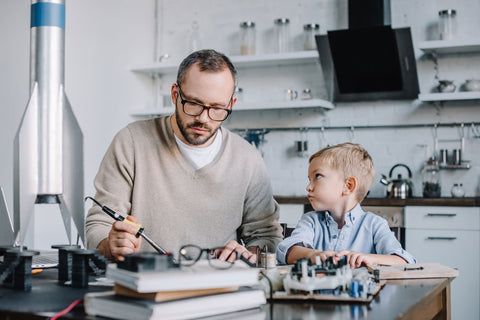
Figure 7: Father and son soldering a circuit board
The conventional type of SSolder consists of a solder wire on a spool. Nonetheless, there are numerous other types based on the form factor classification. They include:
Solder pellets、Solder strips、Solder foil、Solder rods、Solder pastes、Solder ingots、 Solder rings、Brazing solder bars、Solder washers、Solder spheres
Solder washers will be standard in electronic projects.
Types of Solder by Application
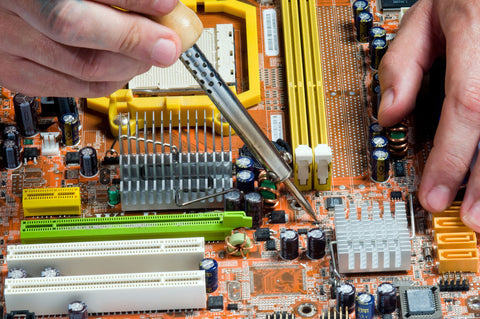
Figure 8: Soldering a Circuit Board
The two main uses of solders are in plumbing and electronics applications. Nonetheless, soldering operation is not limited to the two applications only. For instance, aircraft solder is helpful in selective soldering in planes.
Also, an automotive SSolder is imperative in repairing vehicles’ coolant heat exchangers. Additionally, Solder is useful in household uses. You’ll also find electrical soldering in some hobbies like stained glass manufacturing.
Note that some metals require special soldering due to oxidation during soldering. In such uses, you’ll find specialized solderings such as cast iron solder and aluminum solder.
Q&A
- What is the best solder for electronics?
Lead-free rosin core solder is ideal for a soldering job involving electronics.
- What is the difference between silver solder and regular solder?–
Silver solder will have approximately 45% silver and can be lead-free or lead-based. Essentially, silver SSolder will solve the silver migration problem. On the other hand, a regular SSolder is weaker than silver solder. Additionally, it has a lower melting point than silver solder.
- Can I Use Plumbing Solder for Electronics?-
It is not right to use plumbing solder for electronics. Essentially, plumbing solder is an acid-based flux. On the other hand, electronics solder is rosin core flux. Thus, the acid in the change will be harmful to the wiring. Also, it will prompt a connection failure.