PCB was born in 1936. The United States used this technology extensively in military radios in 1943; since the mid-1950s, PCB technology has been widely adopted. At present, PCB has become the “mother of electronic products”, and its application has almost penetrated into various terminal fields of the electronics industry, including computers, communications, consumer electronics, industrial control, medical instruments, defense and military, aerospace and many other fields.
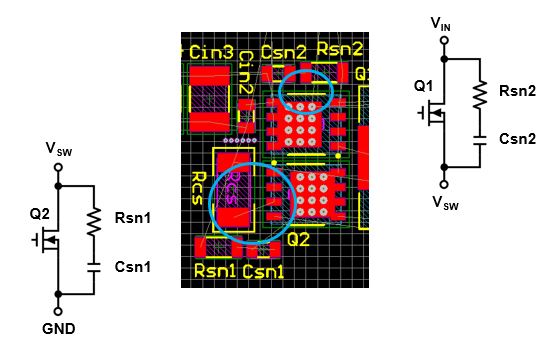
PCB have evolved from single layers to double-sided, multi-layer and flexible, and still maintain their respective trends. Due to the continuous development of high precision, high density and high reliability, the volume is reduced, the cost is reduced, and the performance is improved, so that the printed board still maintains a strong vitality in the development of electronic equipment in the future.
So how is the PCB designed? After reading the following seven steps, you will understand:
1. Preparation in advance
Includes preparation of components libraries and schematics. Before proceeding with PCB design, first prepare the schematic SCH component library and PCB component package library.
The PCB component package library is preferably built by the engineer based on the standard size of the selected device. In principle, the component package library of the PC is first established, and then the schematic SCH component library is established.
The PCB component package library has higher requirements, which directly affects the PCB mount; the schematic SCH component library requirements are relatively loose, but we need to take care to define the pin attributes and the correspondence with the PCB component package library.
2. PCB structure design
According to the determined board size and various mechanical positioning, draw the PCB frame in the PCB design environment, and place the required connectors, buttons/switches, screw holes, assembly holes, etc. according to the positioning requirements.
Fully consider and determine the layout area and non-layout area (such as the extent of the screw hole is a non-layout area).
3, PCB layout design
The layout design is to place the parts in the PCB frame according to the design requirements. Generate a network table (Design→Create Netlist) in the schematic tool, and then import the network table (Design→Import Netlist) in the PCB software. After the network table is successfully imported, it will exist in the software background. Through the Placement operation, all parts can be called out, and there is a flying line prompt connection between each pin. At this time, the device can be laid out.
PCB layout design is the first important process in the entire PCB design process. The more complicated the PCB board, the better the layout can affect implementation of the entire lay out.
The layout design relies on the circuit board designer’s circuit foundation and design experience, which is a high level requirement for circuit board designers. The primary circuit board designer has a shallow experience who is suitable for small module layout design or PCB layout design tasks with low difficulty.
4. PCB layout line design

PCB layout line design is the most labor-intensive process in the overall PCB design, directly affecting the performance of the PCB.
In the PCB design process, layout line generally has three realms:
The first is layout work, which is the most basic entry requirement for PCB design;
Secondly, the electrical performance is satisfied. This is a standard for measuring whether a PCB board is qualified. After the layout is completed which is carefully adjusted to achieve the best electrical performance.
Once again, it is neat and beautiful, chaotic and uncluttered layout, even if the electrical performance is passed, it will bring great inconvenience to the later reformation and testing and maintenance. The layout requirements are neat and uniform, and there is no rule in the vertical and horizontal.
5, Layout optimization and silk screen placement
“PCB design is not the best, only better”, “PCB design is the art of a defect”, mainly because PCB design needs to achieve all aspects of hardware design needs, and individual needs may be conflicting,You can’t have your cake and eat it too
For example, a PCB design project needs to be designed into a 6-layer pcb board after evaluation by the board designer, but the product hardware must be designed as a 4-layer board due to cost considerations, then only the signal shielding ground layer can be sacrificed, resulting in adjacent layout. Signal crosstalk between layers increases and signal quality decreases.
The general design experience is that the time to optimize the layout is twice the time of the initial layout. After the PCB layout optimization is completed, post-processing is required. The first thing to deal with is the silk screen mark on the PCB board surface. The bottom screen silk screen characters need to be mirrored during design to avoid confusion with the top screen printing.
6.Network DRC inspection and structural inspection
Quality control is an important part of the PCB design process. The general quality control methods include: design self-inspection, design mutual inspection, expert review meeting, special inspection and so on.
The schematic and structural element diagrams are the most basic design requirements. The network DRC inspection and structural inspection are to confirm that the PCB design meets the two input conditions of the schematic netlist and the structural element diagram.
General circuit board designers will have their own accumulated design quality checklist, which is partly based on the specification of the company or department, and the other part is summarized in its own experience. Special inspections include Valor inspection and DFM inspection of the design. These two parts focus on the PCB design output back-end processing lithography files.
7. PCB manufacture board
Before the PCB is formally processed, the board designer needs to communicate with the PE of the PCB supplier board to answer the manufacturer’s confirmation of the PCB board processing.
These include, but are not limited to, PCB board model selection, line layer line width adjustment, pcb impedance control adjustment, PCB stack thickness adjustment, surface treatment process, aperture tolerance control and delivery standards.
The above is the entire process of PCB design.